Innovation & Digital Transformation
Logan Aluminum is comprised of a knowledgeable workforce, commitment to continuous improvement, and leading technologies and innovation. Some of our current efforts include digitization, enhancing our visualization and dashboarding to support predictive analytics, Artificial Intelligence (AI) Bots, enhancing mobility, as well as many other digital technologies.
Recycle Furnace
Used beverage cans and other scrap are shredded and melted, then transferred by crucible to be added to a melting furnace.
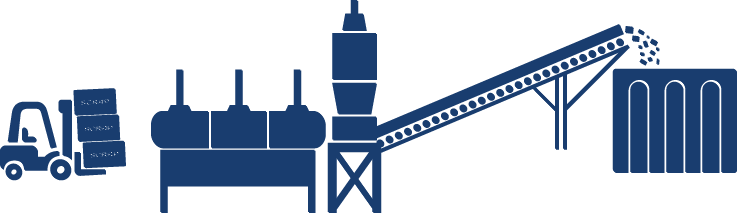
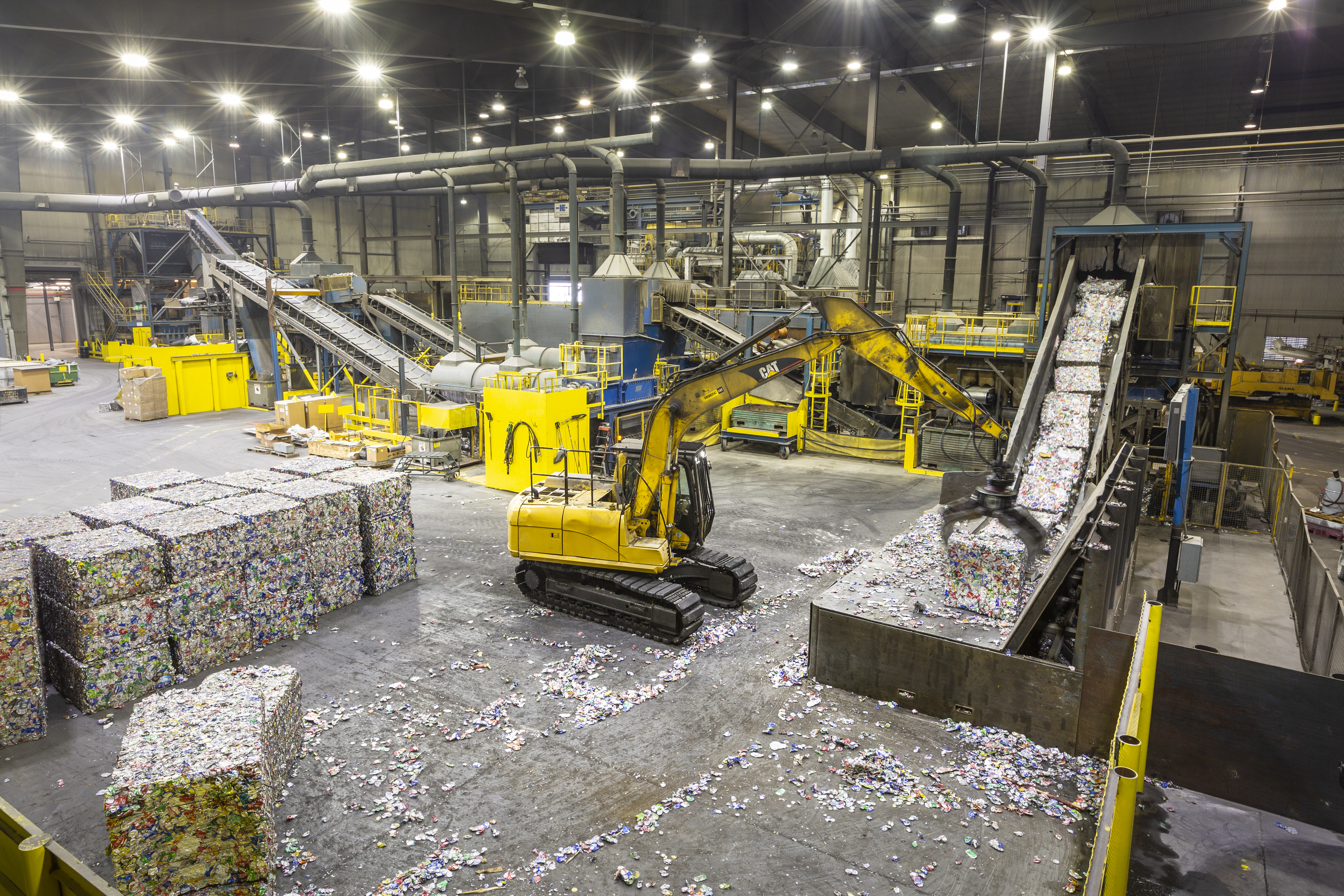
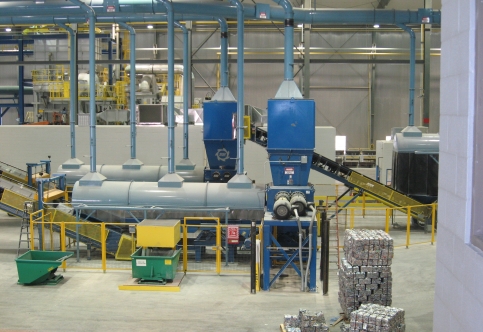
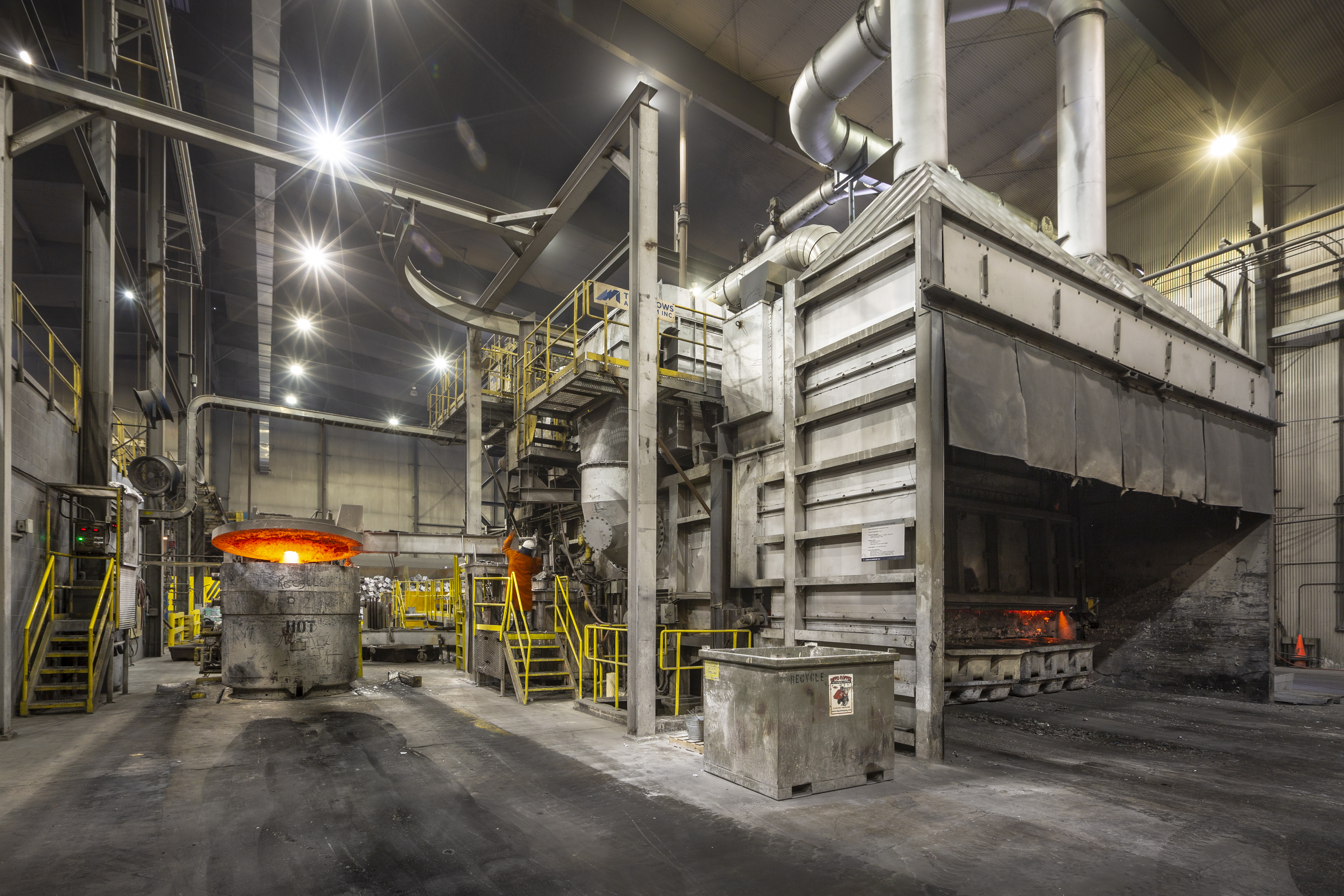
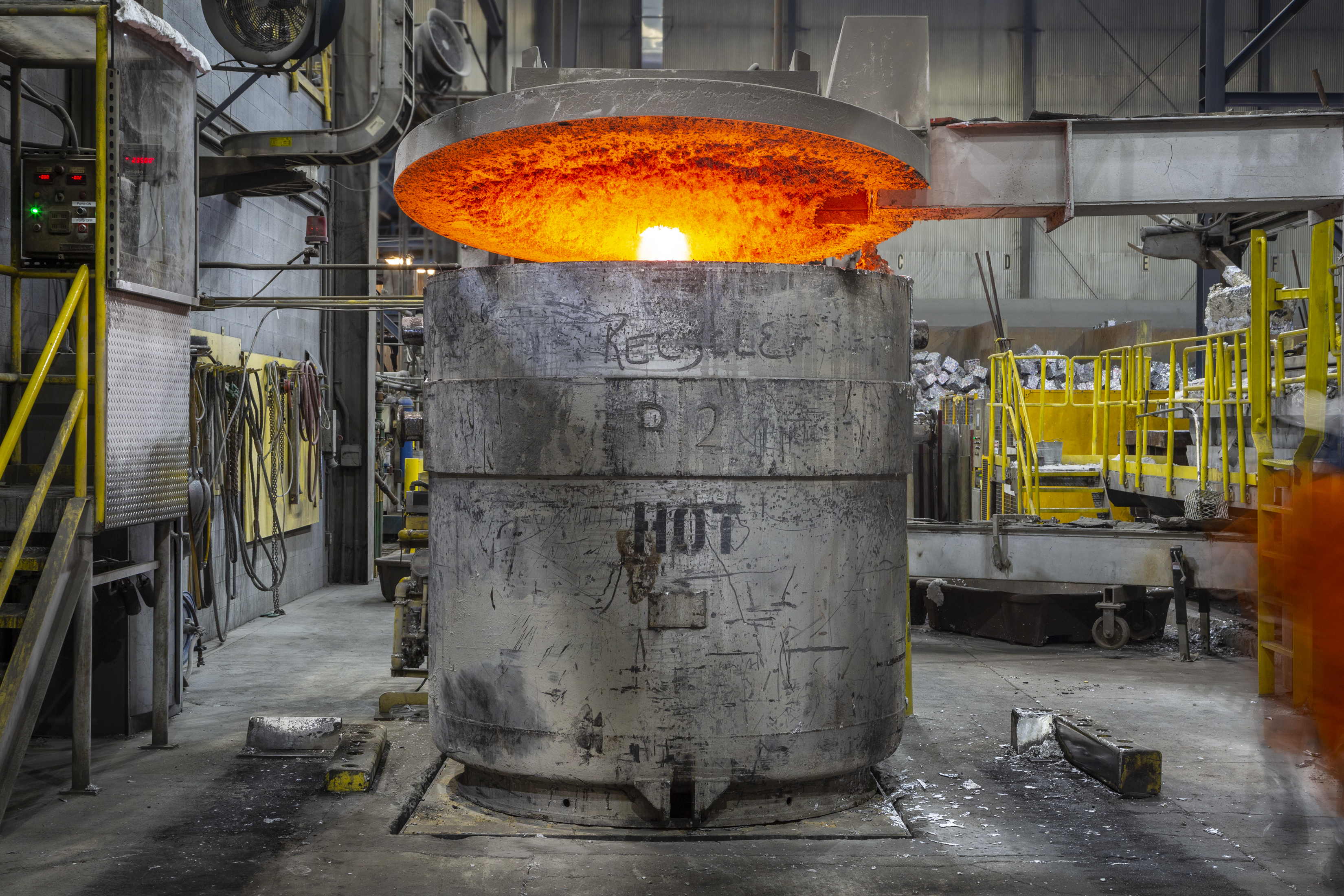
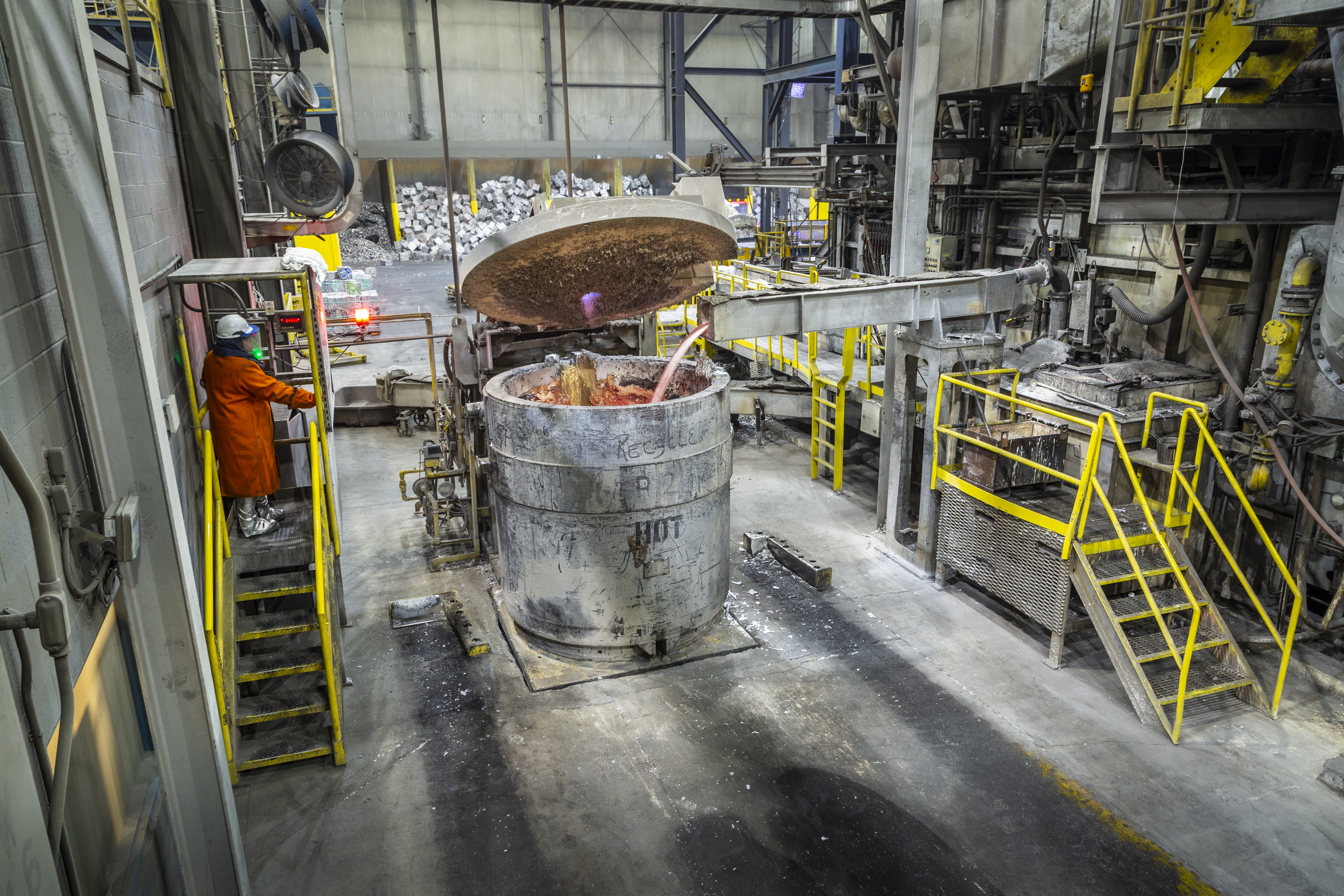

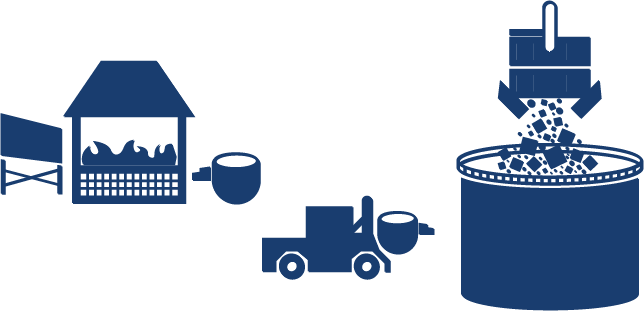
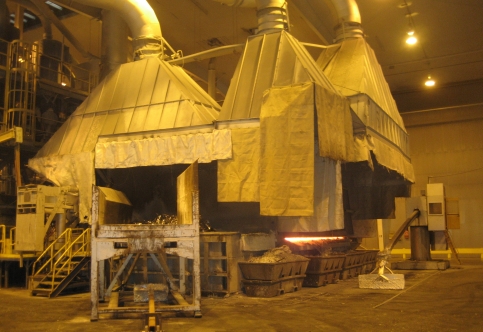
Swarf Furnace
Light gauge or thin scrap metal is melted then transferred by crucible to be added to a melting furnace.
Remelt Chemical Analysis
Remelt uses automated optical emission spectrometers to measure the chemistry of aluminum at various process steps in the remelt department.
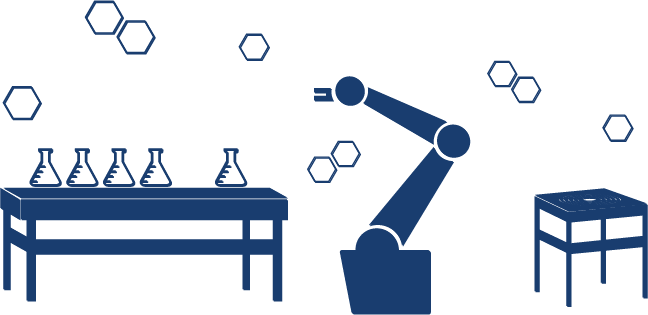
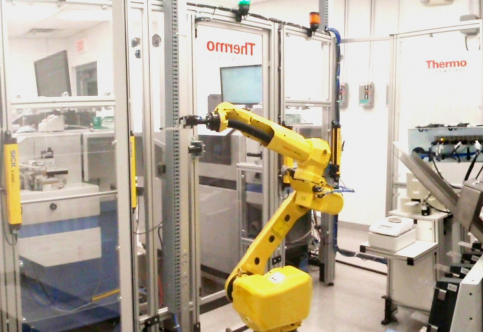
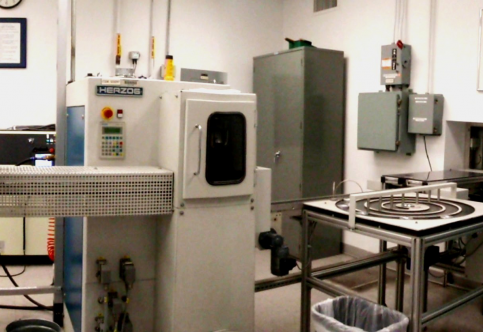
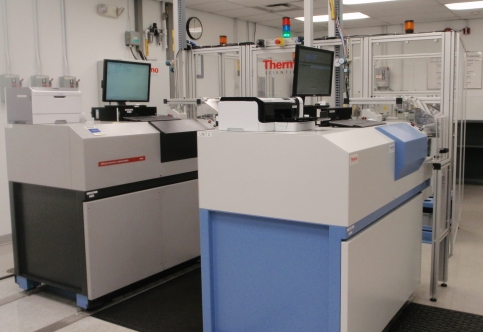
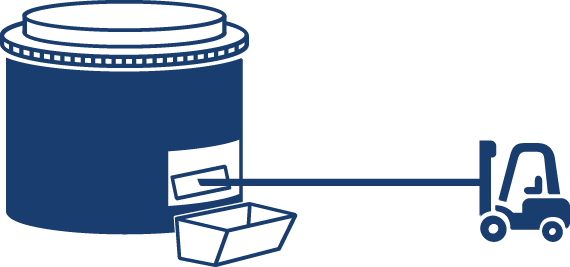
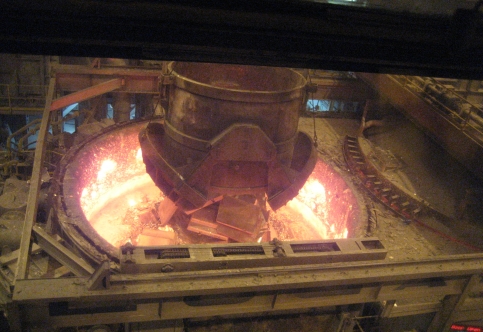
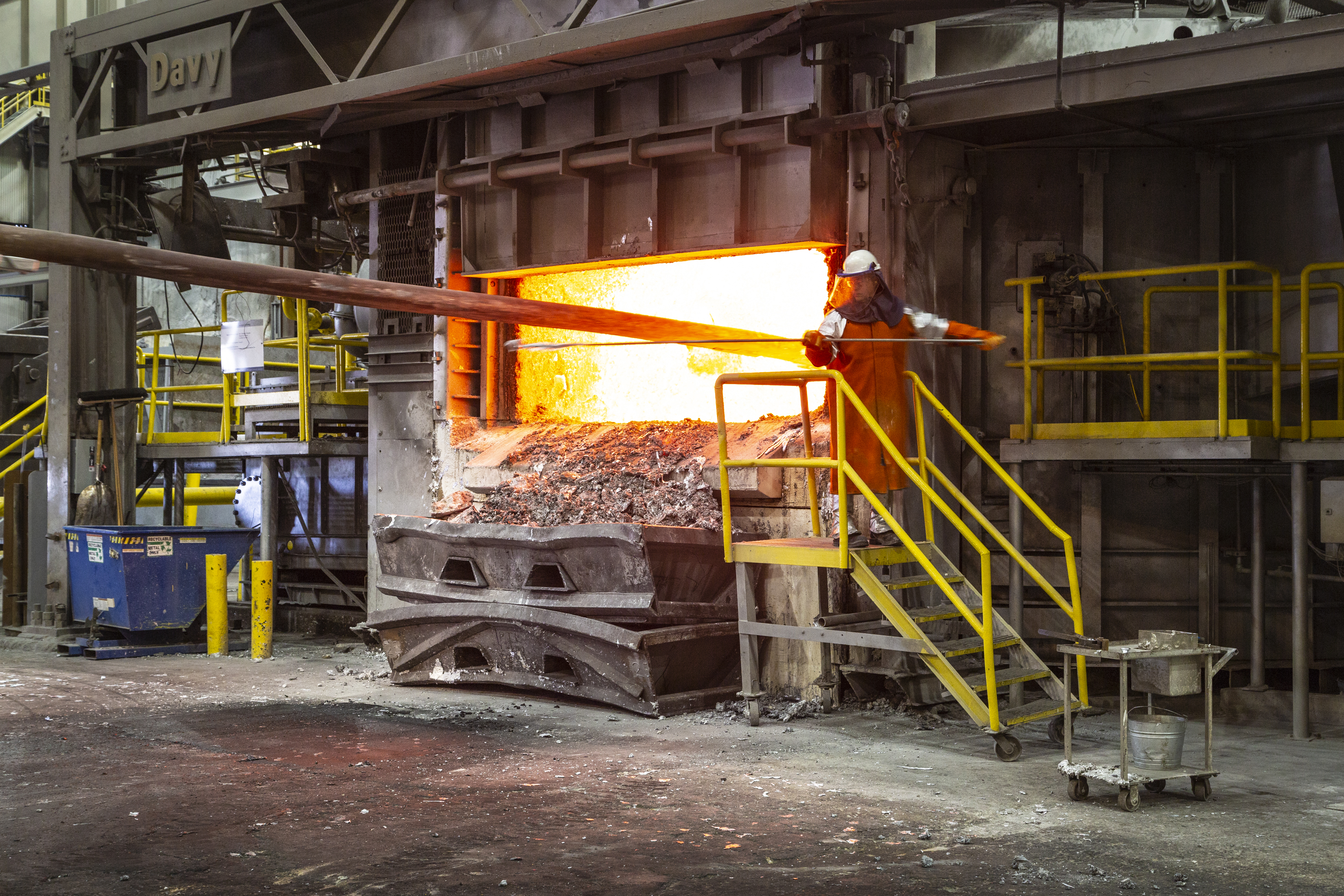
Melting Furnace
Solid metal is melted and mixed with molten metal from the Swarf and Recycle furnace. Once melted the molten metal is transferred to the holding furnace.
Holding Furnace & Casting
Molten metal in the holding furnace is prepared for casting. The casting system produces solid ingots weighing up to 65,000 lbs. After casting the ingots are sent to the Hot Mill for further processing. Each ingot can weigh as much as 17 compact cars.
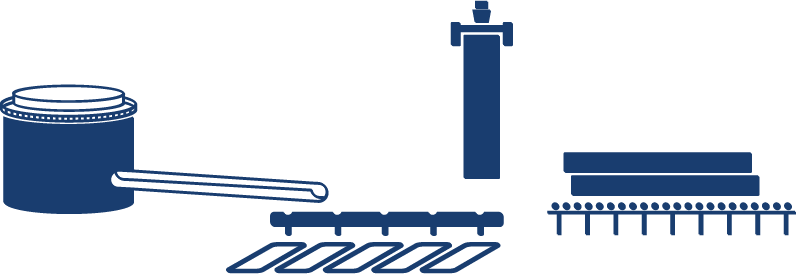
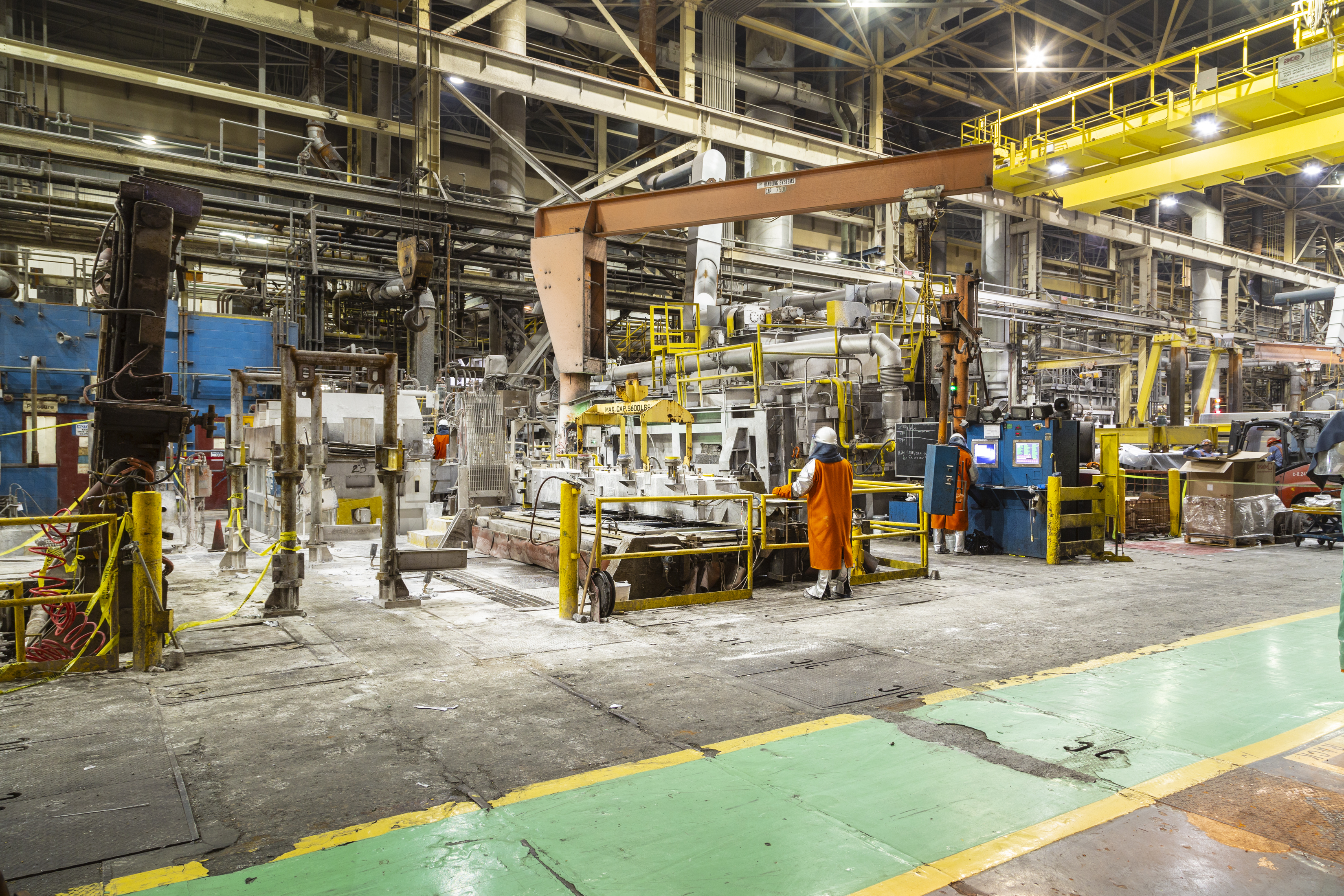
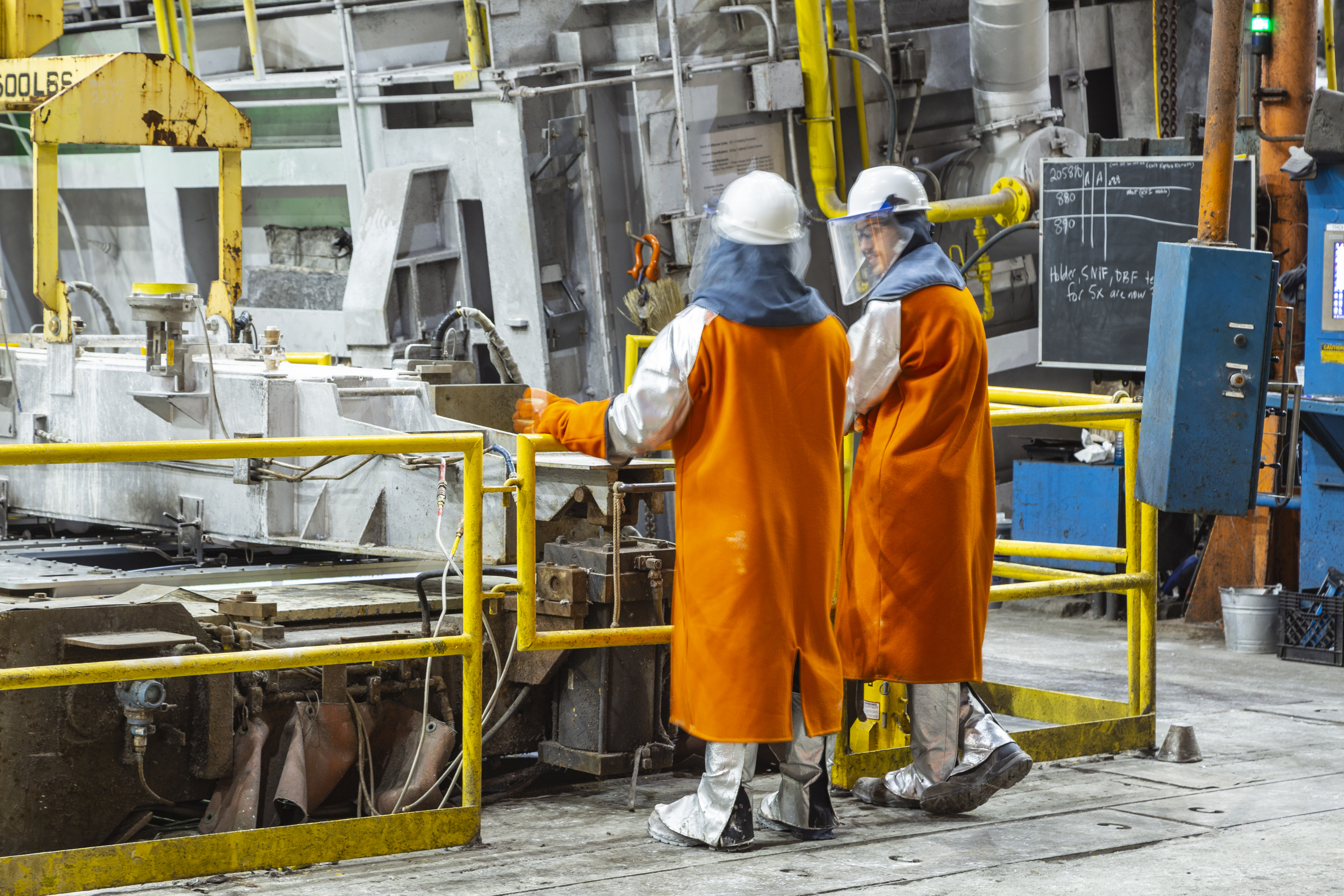
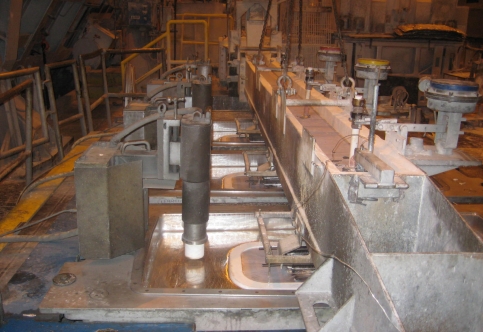
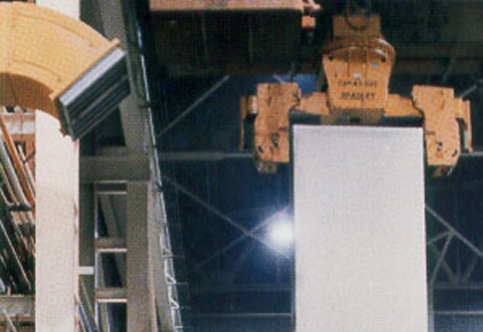
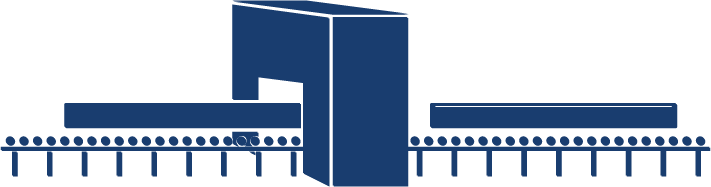
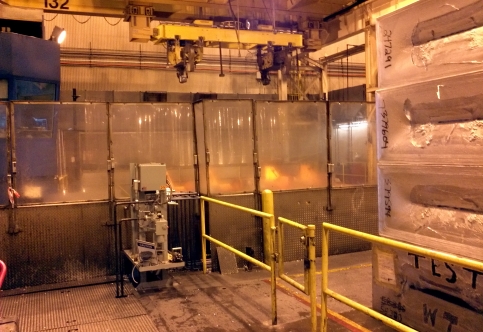
Ingot Scalper
Ingots from the Caster are scalped or machined on the surfaces that will be rolled in the hot mill. About one-half of an inch is removed from the rolling surfaces.
Ingot Pusher Furnace
The pusher furnace heats, softens, and conditions the scalped ingots for the hot rolling process.

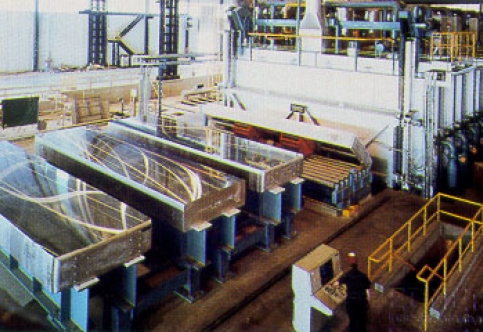
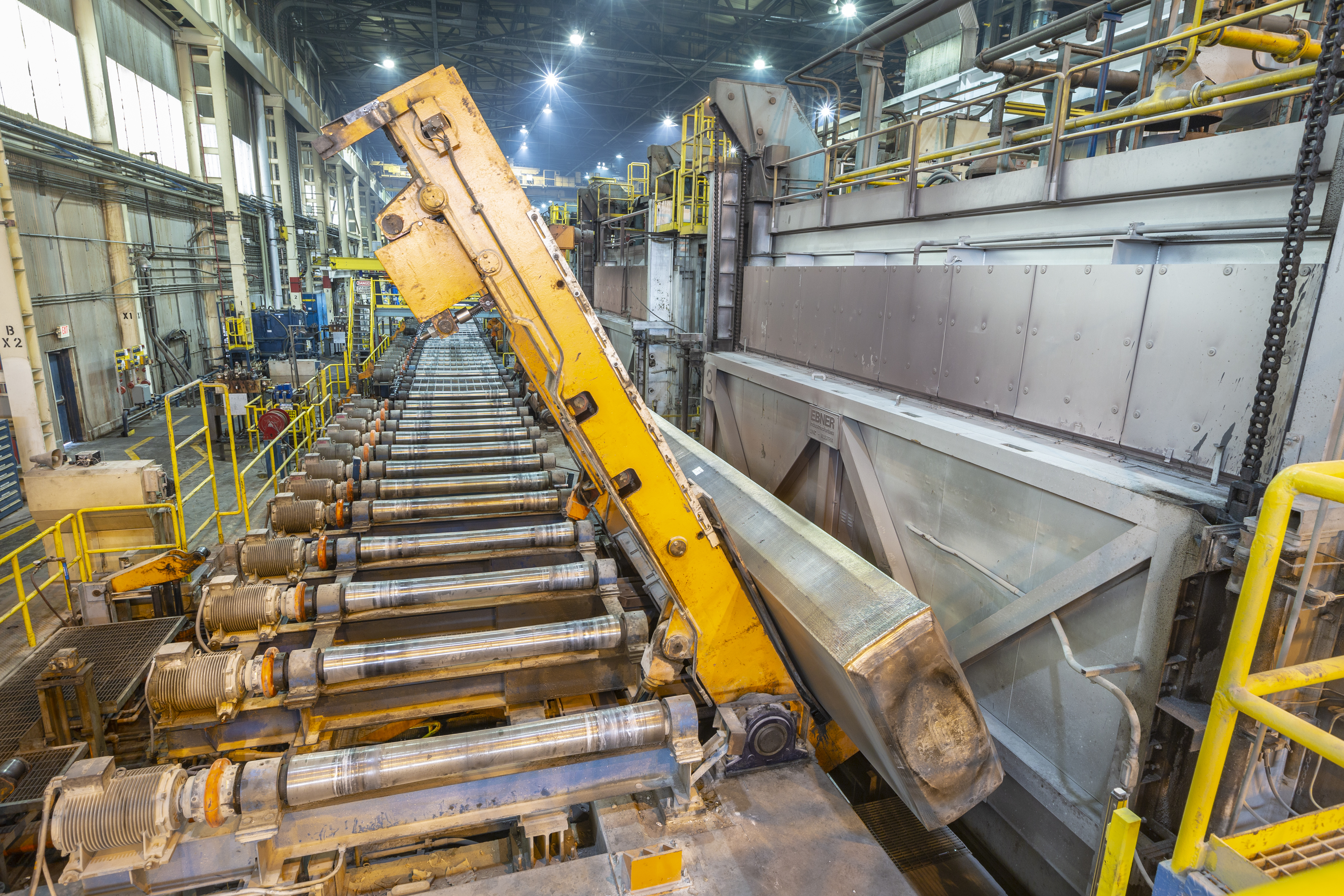
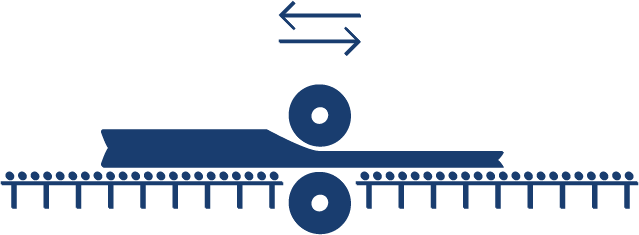
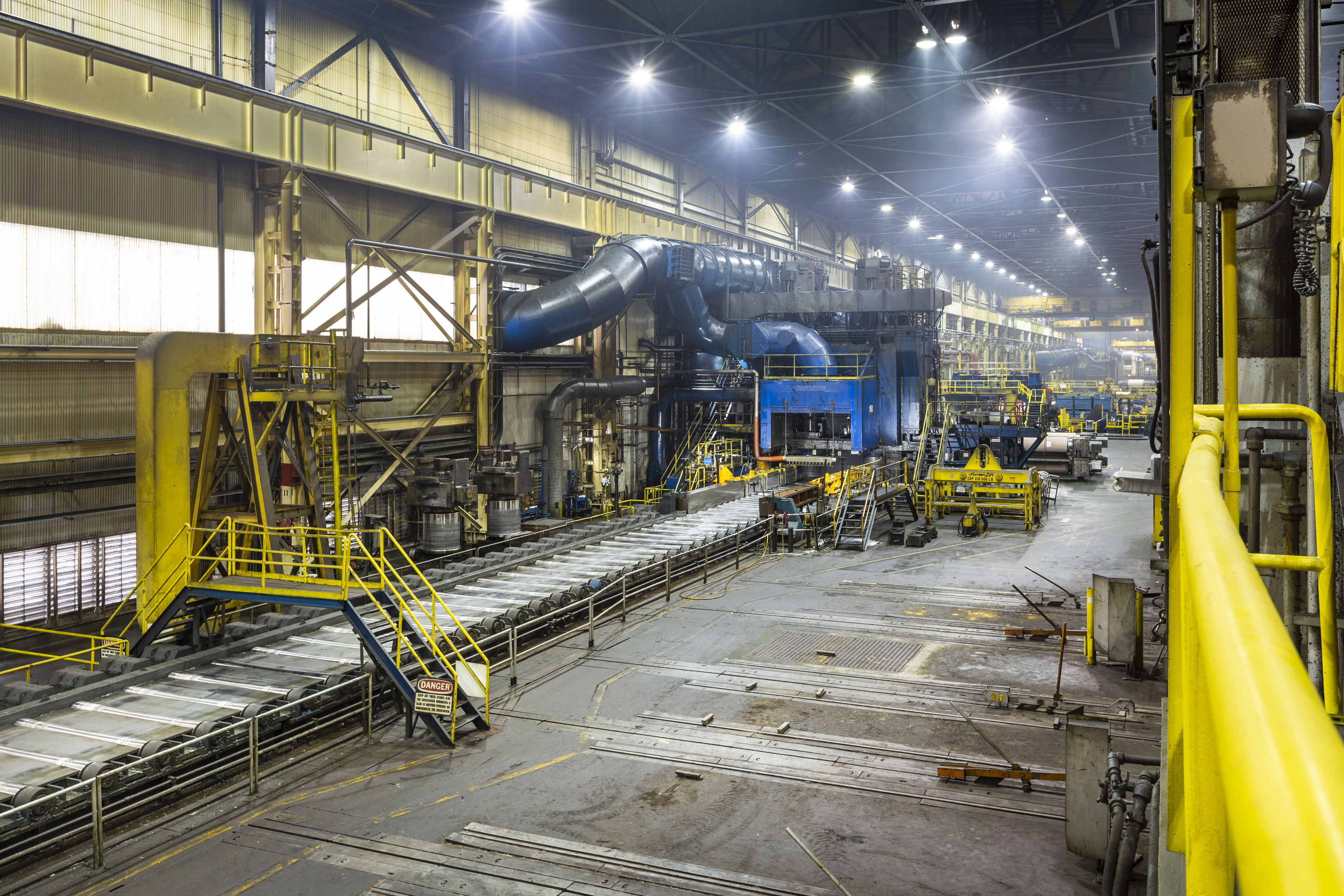
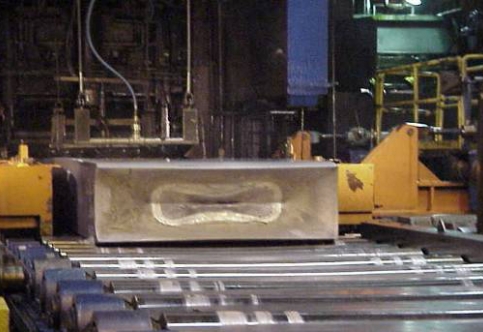
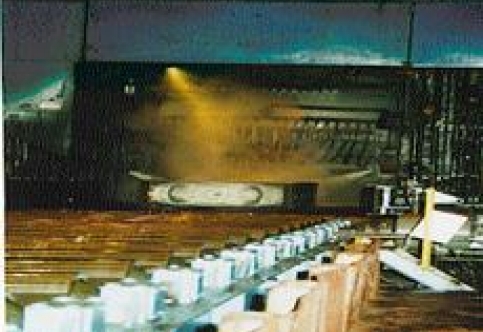
Hot Mill - Reversing Mill
The reversing mill rolls an ingot back and forth from a thickness of about 30 inches to about 1 inch. The resulting slab is rolled to the finishing hot mill operation.
Hot Mill - Finishing Mill
The finishing mill rolls the 1 inch slab from the reversing mill into a coil of aluminum sheet that is about one-tenth of an inch thick. The resulting “hot band” coil is then moved to a cooling area in preparation for cold rolling.
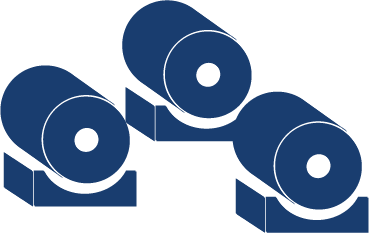
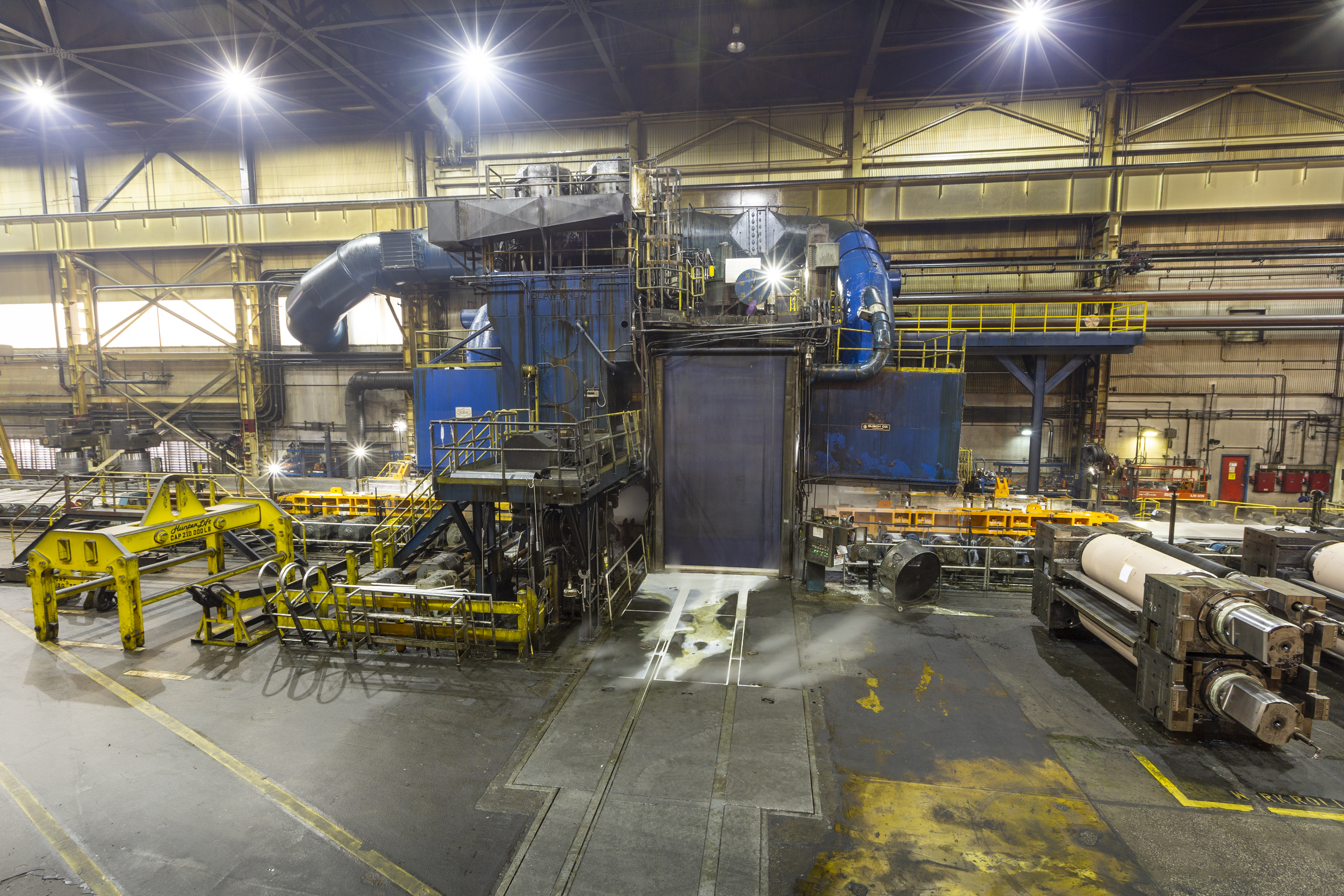
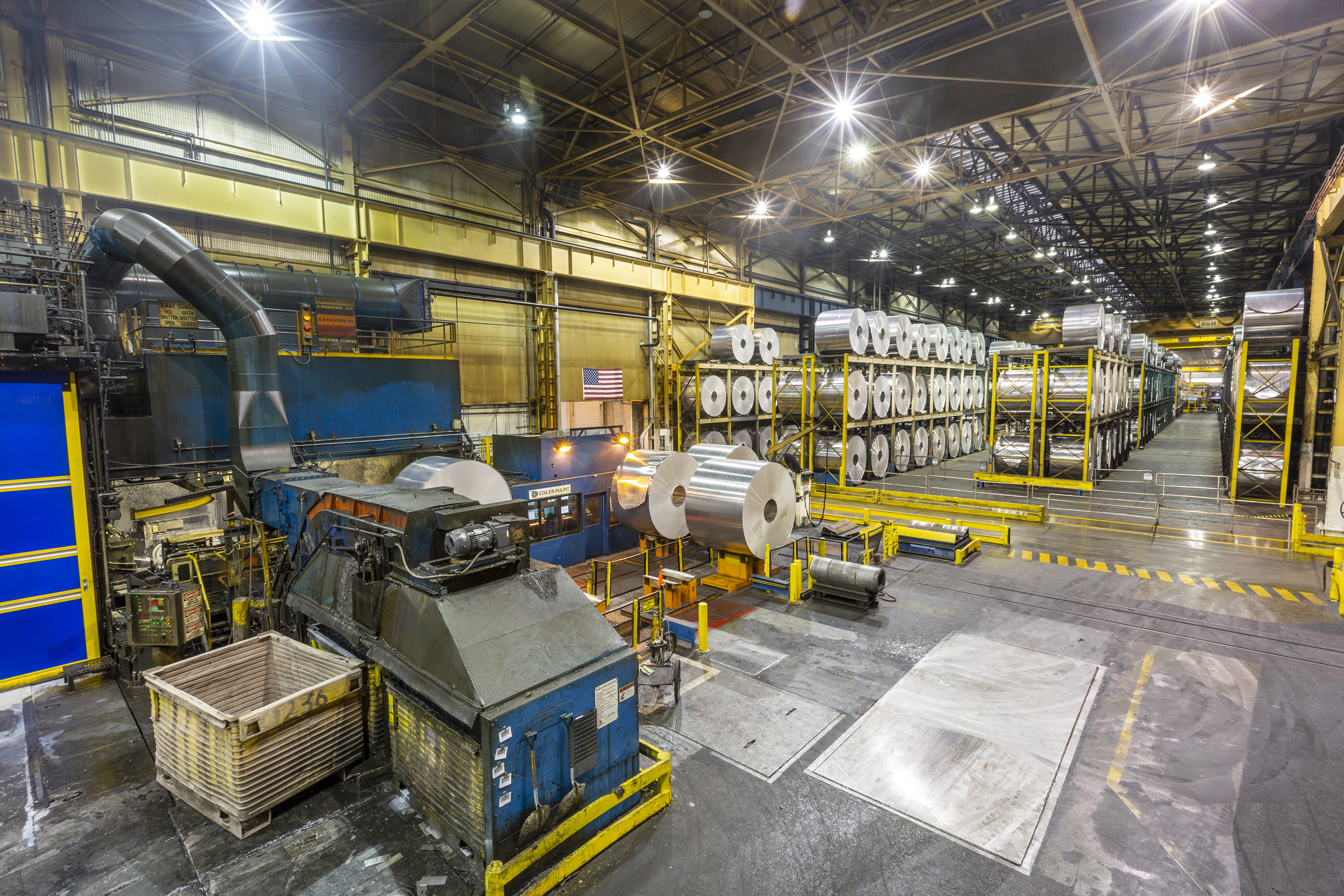
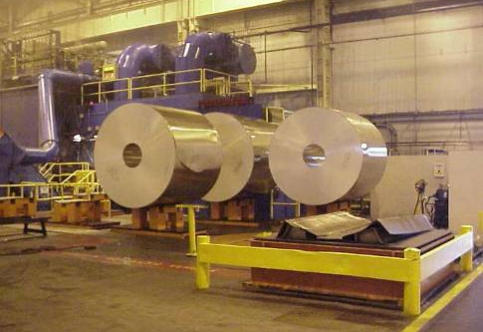
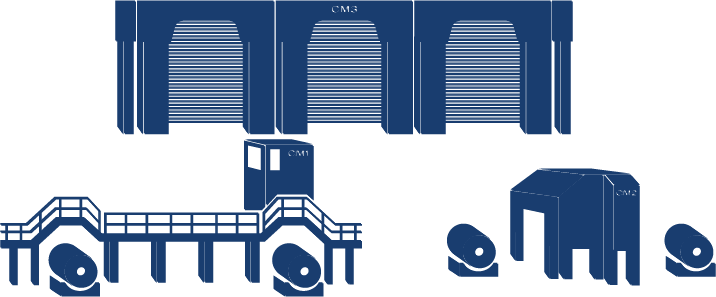
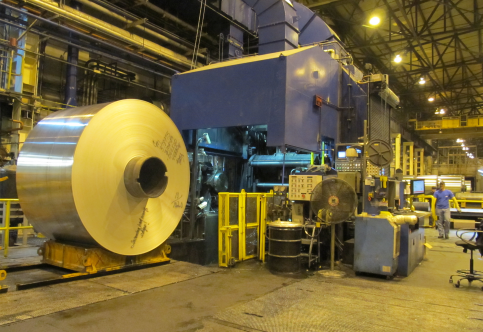
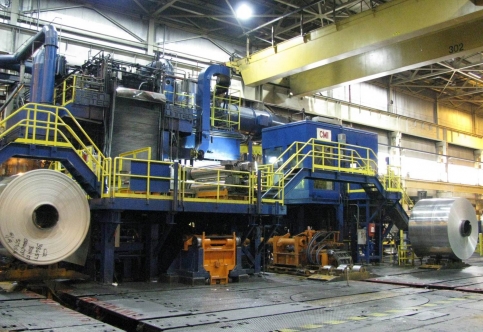
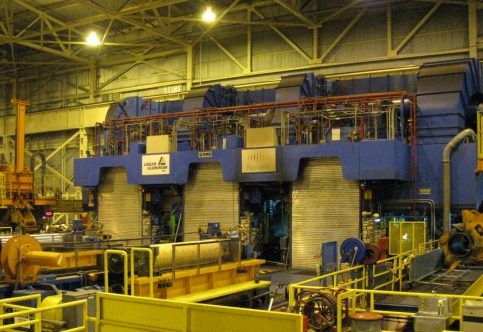
Cold Mill
There are three rolling mills in the cold mill. They are the heavy cold mill, light cold mill and the 3-stand tandem mill. They all perform the same task of rolling the hot band from the hot mill to the finished sheet thickness. The finished thickness is about the thickness of a sheet of paper. If the finished coil were rolled out flat, it would stretch about seven miles!
Tension Leveler
Some products are processed through the tension leveler, that stretches the sheet a few percent to make it very flat.
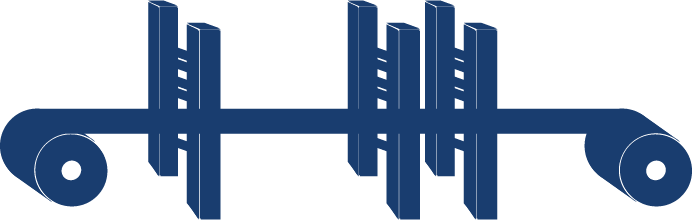
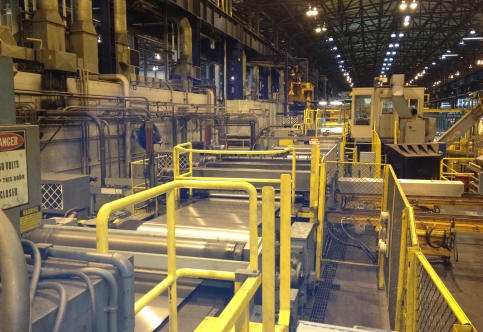
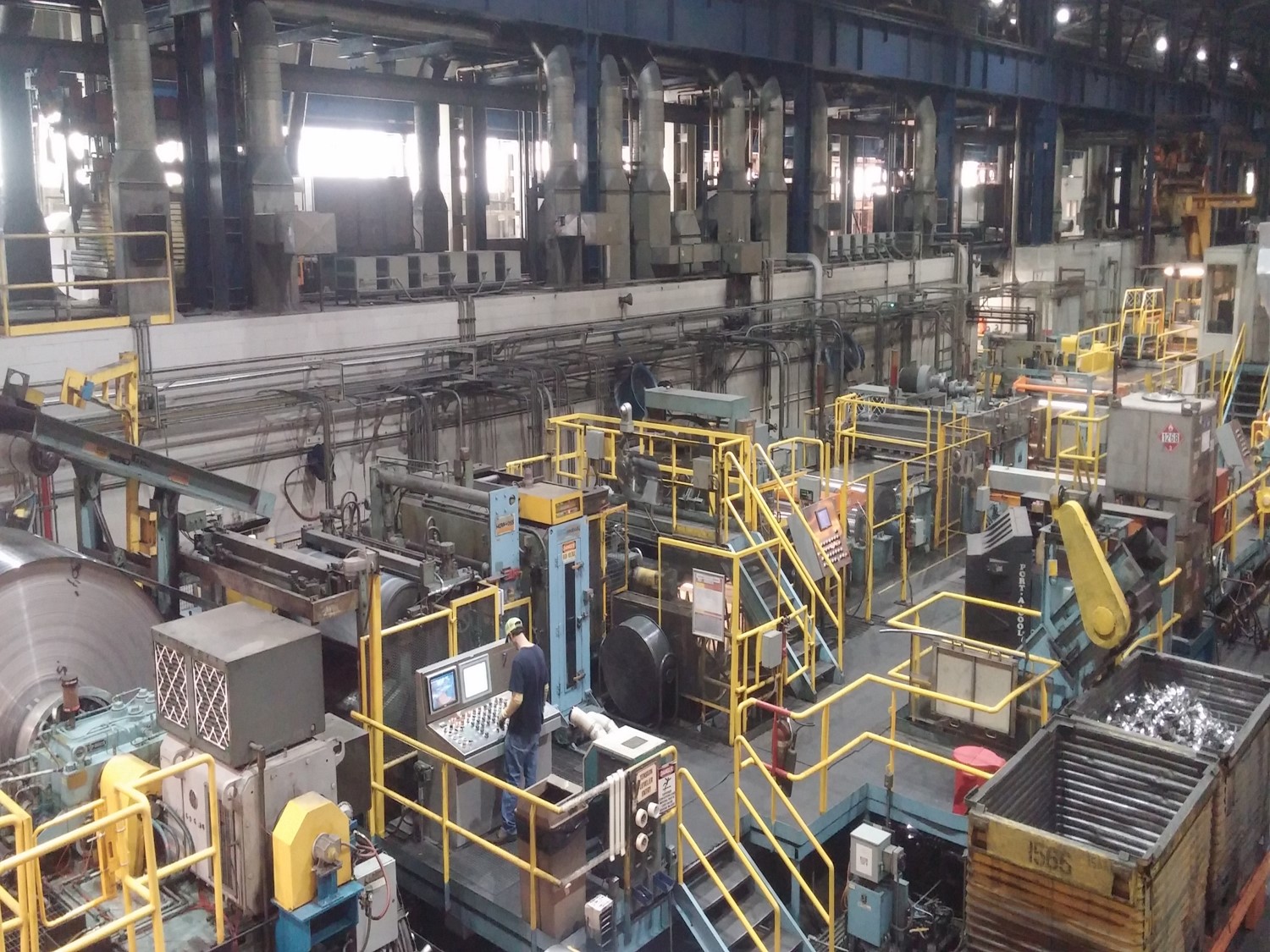
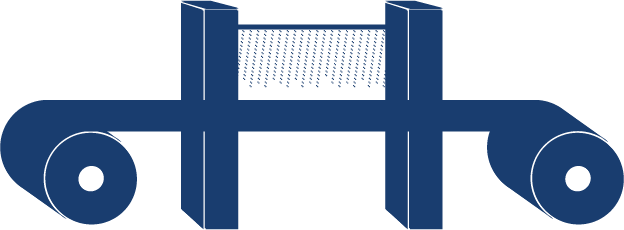
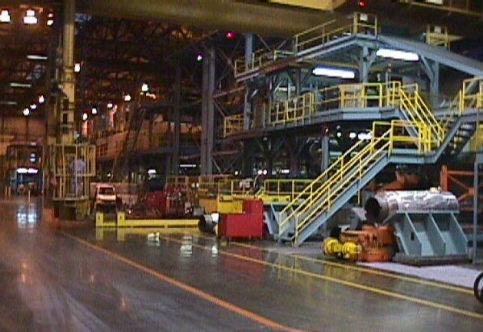
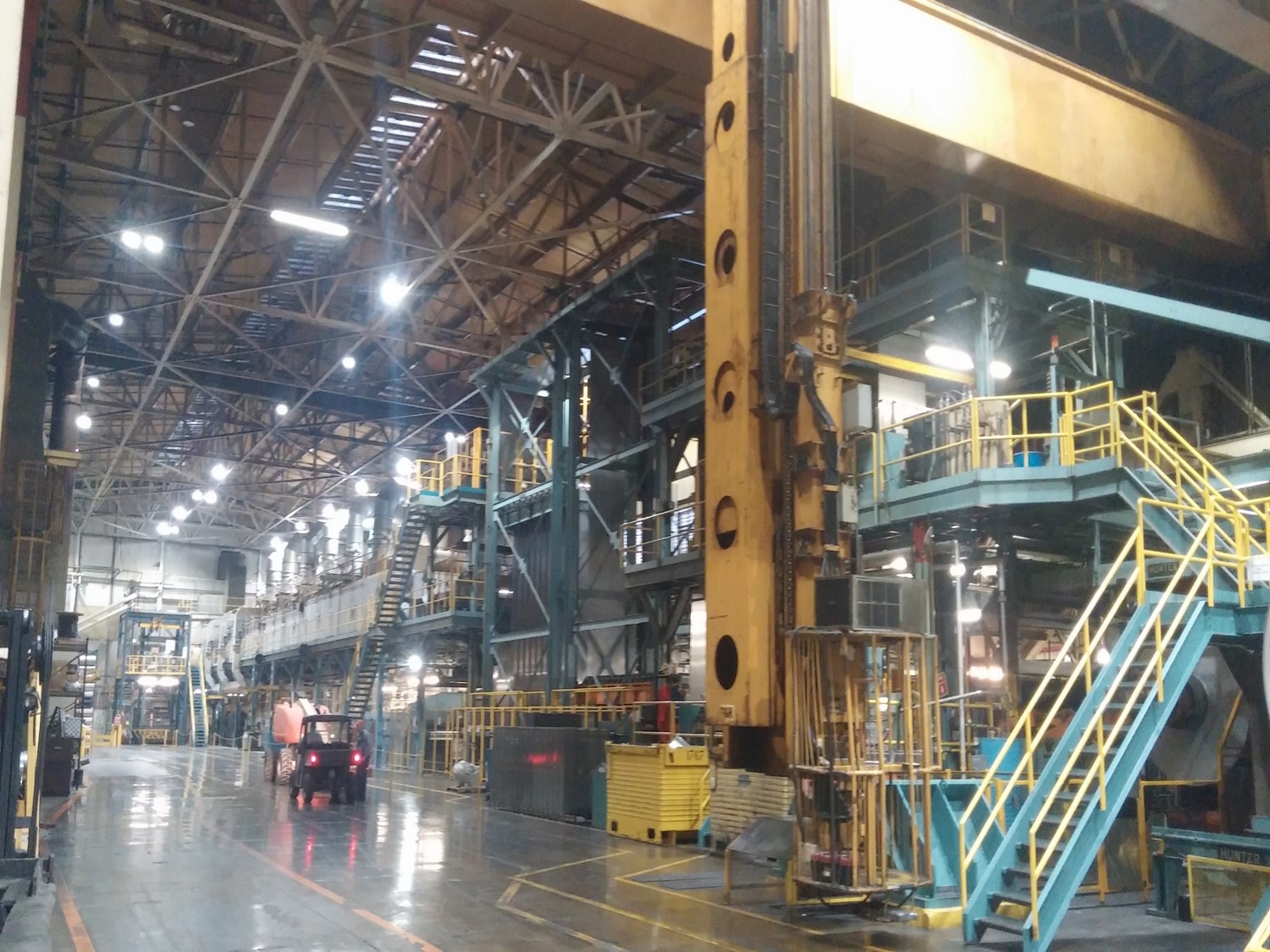
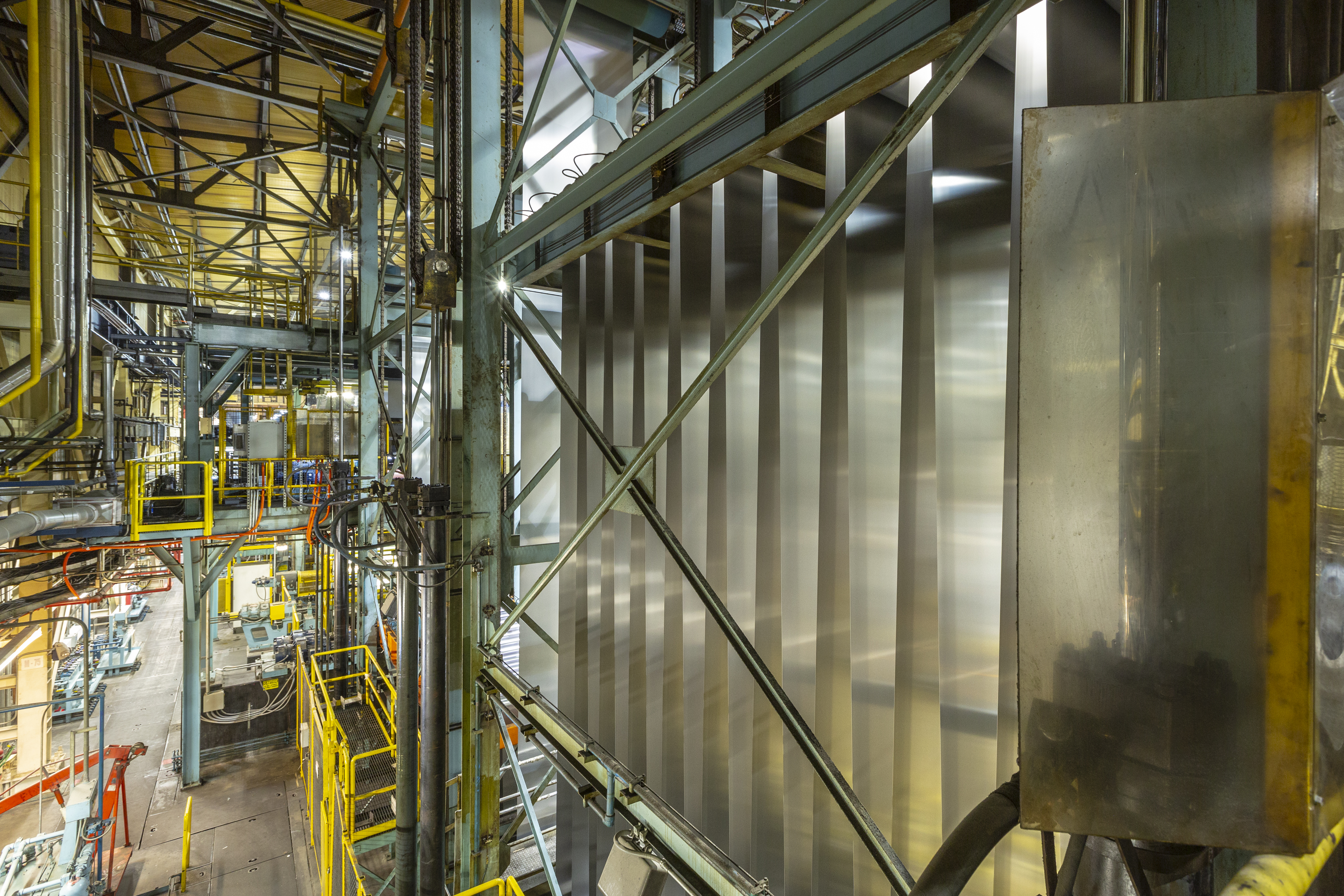
Coating Line
Some products are coated so that when it is used in a beverage can there is a barrier between the aluminum and the beverage.
Level Clean Line
This process levels and cleans the sheet before it is packaged and shipped.
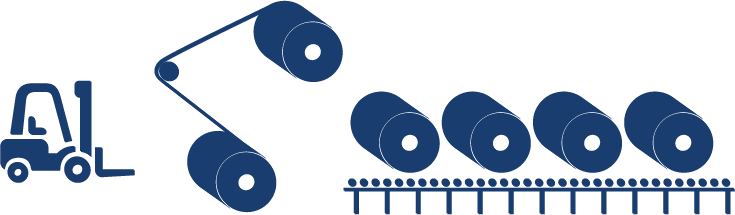
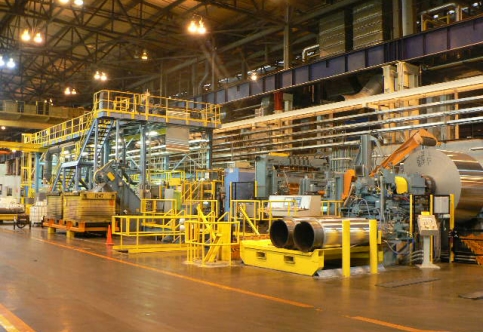
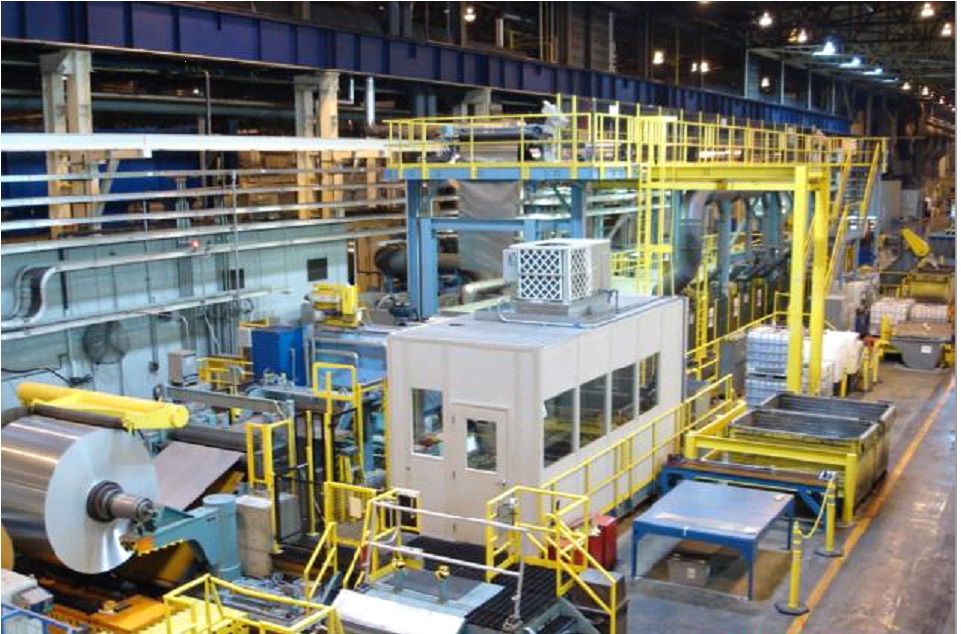
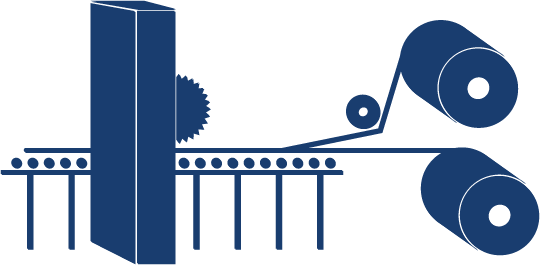
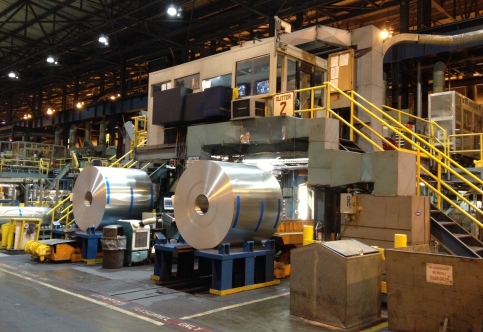
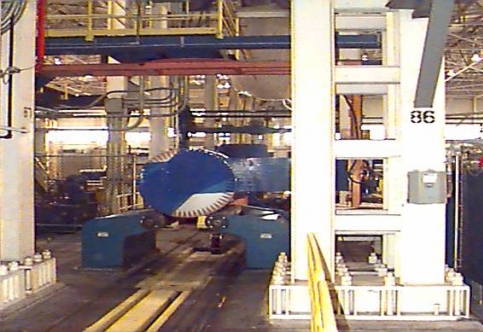
Slitters
This operation cuts the sheet into the width and length the customer requires. From here the product is packaged and shipped.
Packing & Shipping
Once metal is packed, it is transported via truck or rail car to customers.
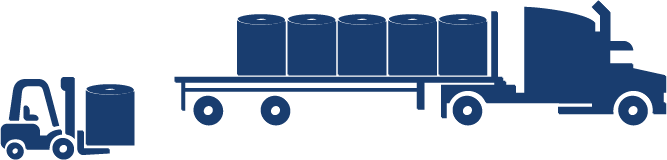
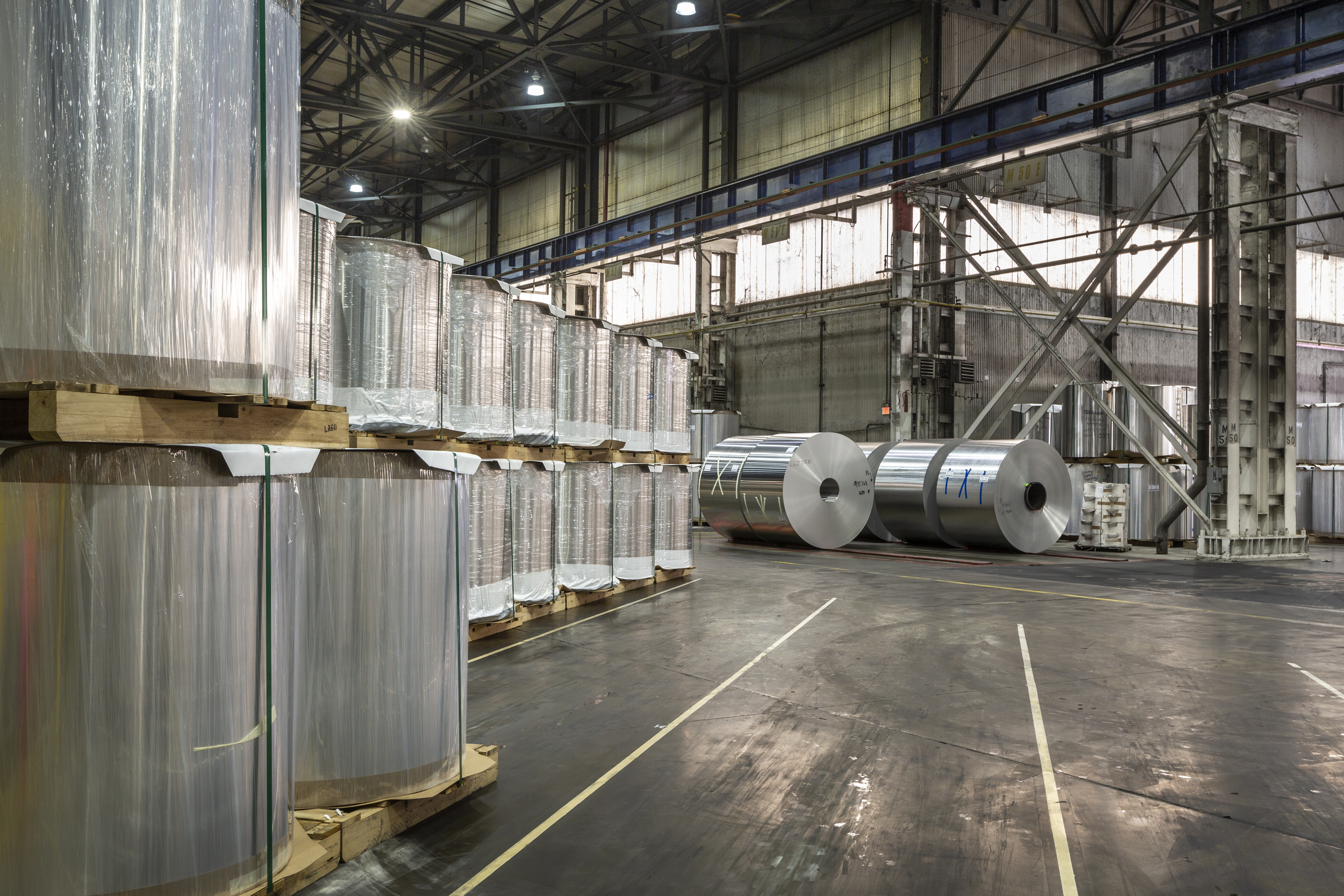
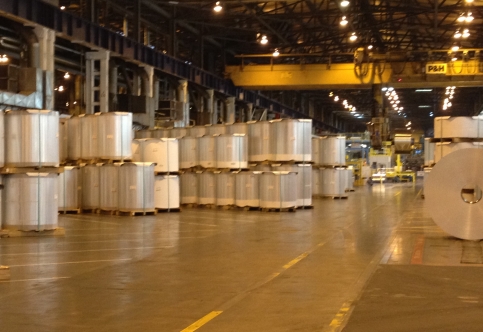